
ETFE in the Chemical Industry: Key Advantages and Uses
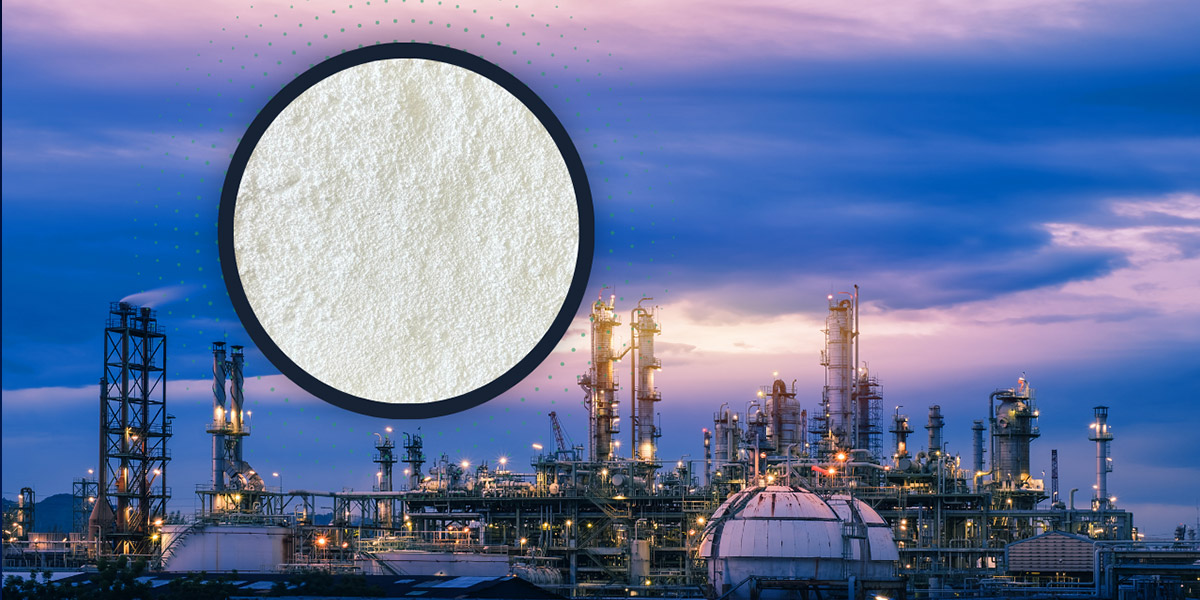
ETFE (Ethylene Tetrafluoroethylene) has been a game-changing factor in the field of chemical applications because of its totally different set of properties, which serve as a backbone in many applications.
ETFE, a fluoropolymer commercialized by DuPont in 1973, is getting great attention presently for its outstanding chemical resistance and thermal stability along with wonderful mechanical strength.
Let us take a look at some of the major advantages and uses of ETFE in the Chemical Industry.
What is ETFE?
ETFE is a partially fluorinated copolymer of ethylene and tetrafluoroethylene.
Its molecular structure is described by the chemical formula: (C4H4F4)n, where sequences of ethylene and TFE monomers alternate.
This structure allows ETFE to have crystallinity in the order of 40% to 60% and a melting temperature between 225°C and 300°C, based on the ratio of comonomer and methods involved in processing.
Key Advantages of ETFE
Applications in the Chemical Industry
Coatings and Linings
Its very good chemical resistance and high bonding strength make ETFE one of the most appropriate choices for protective coatings and linings in relation to the chemical industry.
Some typical uses include
The density and pinhole-free nature of the melt-processed ETFE films give the material very high safety and chemical resistance.
Even thin ETFE sheets (0.6mm) have shown remarkable corrosion resistance to various acids over extended periods.
Injection Molded and Extruded Products
ETFE's processability allows for the creation of various components crucial to the chemical industry:
Composite Materials
The compatibility of ETFE with other materials enables the development of advanced composite products in such areas as:
Processing ETFE
While ETFE offers numerous advantages, processing conditions need to be taken seriously to reap full benefits from this high-performance fluoropolymer
It's also worth mentioning at this point that process equipment should be fabricated with corrosion-resistant alloys because during processing corrosion compounds may form under high temperatures.
Conclusion
The balance among the attributes of ETFE—chemical resistance, thermal stability, and mechanical resistance—keeps it irreplaceable within the chemical production sector.
From protective linings and coatings to specialized components and packaging, ETFE continues to push the boundaries of what's possible in challenging chemical environments.
As the industry evolves further, we will witness more creative uses for this versatile fluoropolymer, raising efficiency, safety, and durability in chemical processes worldwide.
For cutting-edge fluoropolymer solutions tailored to your chemical industry needs, trust Advecton – your partner in innovation, quality, and expertise for ETFE and other high-performance materials.