
How to Offer or How to Get 20-30% Discounts in PTFE/PFA Lined Pipes, Lined Fittings and Lined Valves
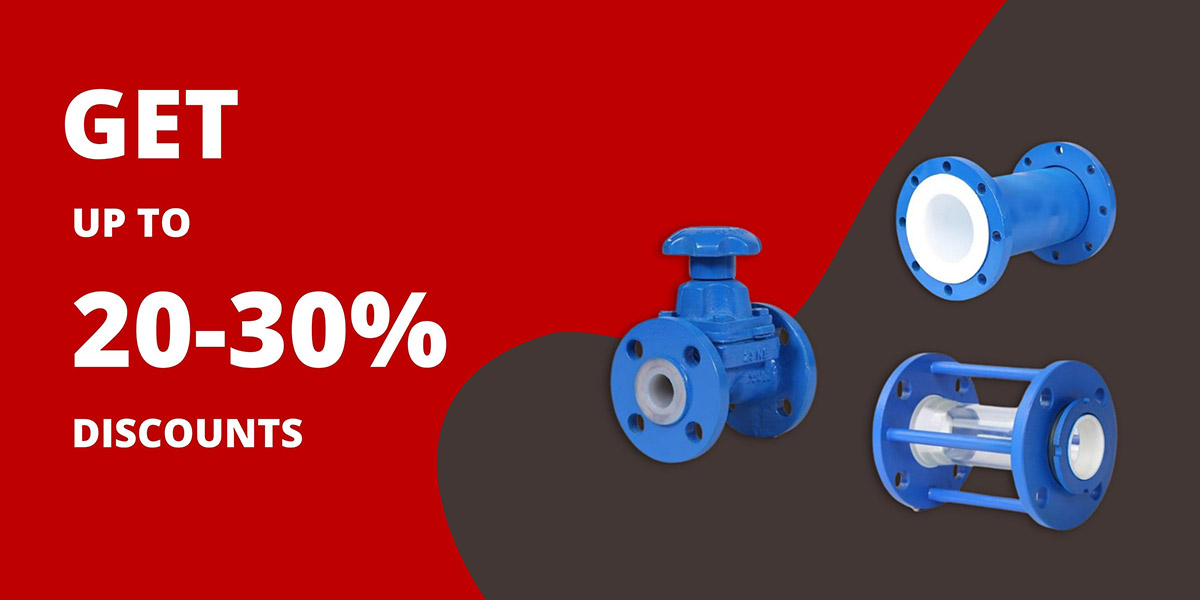
In recent years, market size and demand for processing equipment, mainly glass-lined equipment, PTFE-lined pipes and fittings, PFA, PFA-lined valves and Borosilicate glass equipment, have nearly doubled. These equipment are used in bulk drug processing plants, corrosive chemical processing, high purity applications, general pharma, acids, chemical, and fine chemical industries. For the design and safety of products, there are different standards like ISO9000, ASTM F 1545 & ASME B16.3 already available.
While competition fosters innovation and improvement in the market, it has also led some to adopt practices that attract customers through lower prices and significant discounts. As an integral part of our organisation, we aim to highlight certain cost-reduction techniques and questionable practices prevalent among many companies, particularly in some markets, especially in India.
As manufacturers of PTFE-lined pipes, fittings, and valves for over 20 years, we have noticed an influx of new suppliers offering similar products. This article aims to shed light on some concerning industry practices that prioritise profits over ethics in the manufacturing and supply of critical processing equipment.
Why We Stand Apart
Quality Shortcuts to Reduce Costs
We need to understand that competitive and too-low prices are completely different things basis the malpractices and how readers would accept them. Here, we have summarised some common techniques used by some manufacturers to offer exceptionally low bids:
In RFQ, most of the specifications demand fluoropolymer of top brands, which is almost 30-40% more expensive compared to alternative materials. Even the cost of fluoropolymers is country-specific, like whether that was manufactured in India, China, Japan or the USA. Additionally, top-brand fluoropolymers are mainly expensive due to their properties, brand value or consistency in quality and long life.
In reality, some manufacturers claim to use the specific brand, but ultimately, they use cheaper products of x country, which customers are not aware of. In the documentation, they never come to know what was used and supplied. During negotiation, buyers get satisfied as if they bought gold at the price of steel, hoping that the manufacturer would supply what they had asked for.
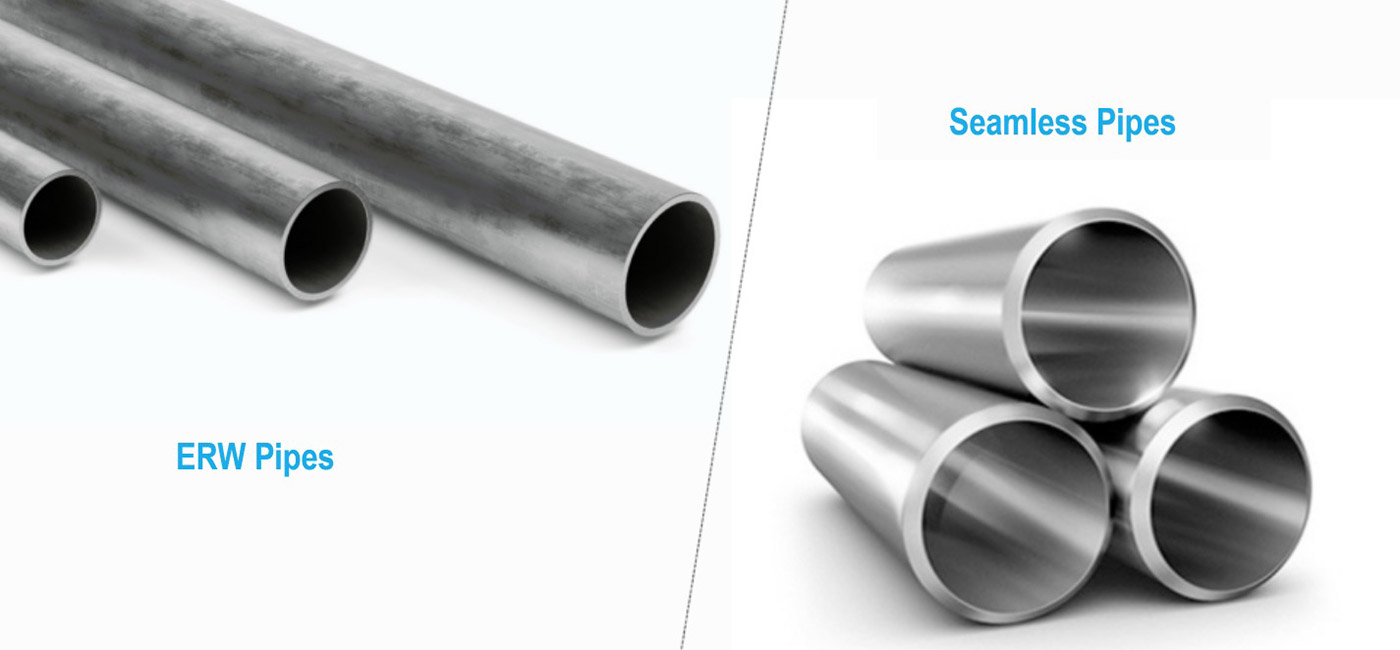
Based on standards, pipes must be seamless and scheduled 40 or above up to fixed diameters, but manufacturers use high-quality ERW pipes with invisible weld joints. Such pipes can turn out absolutely risky in plants where high-pressure materials are operated. This definitely saves huge costs but with compromised quality. Even in some cases, SS 304 is used for orders of SS316 and also other materials like SS202 or lower grades of SS.
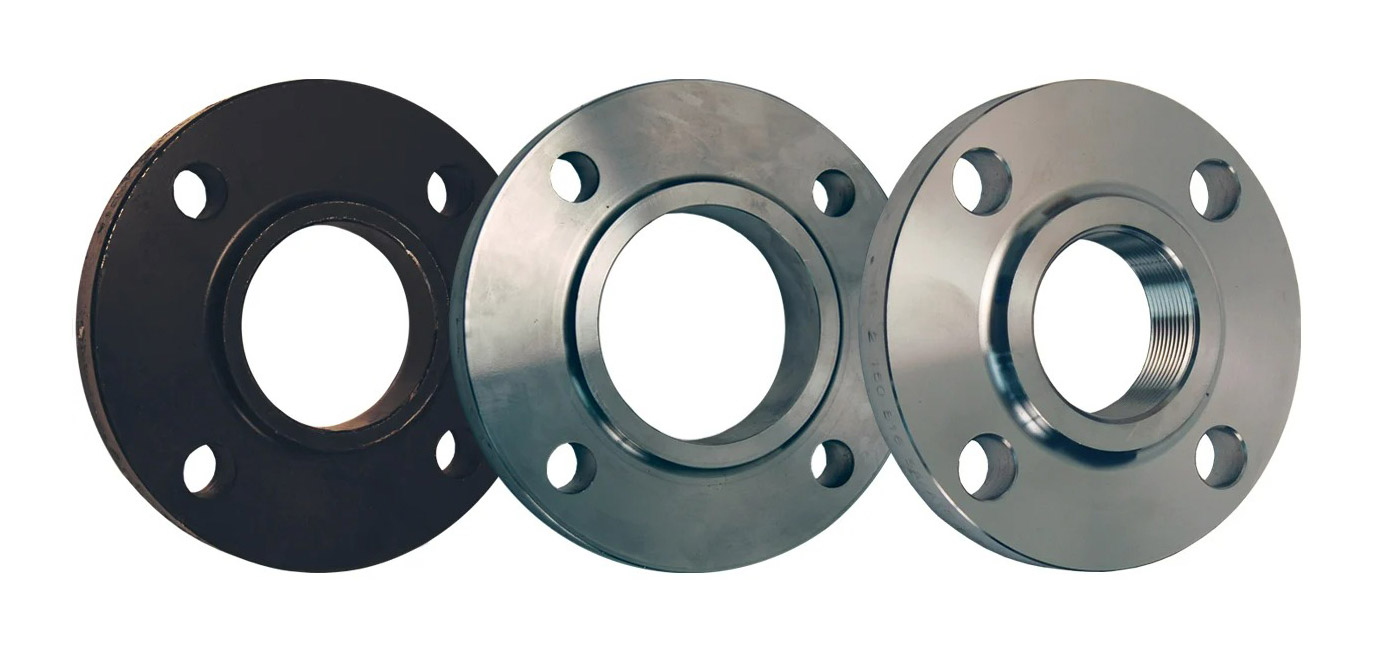
As per specifications, a flange should be of a particular thickness and material. In contrast, some manufacturers are using lower grade or material from scrap to save cost. In fact, they reduce flange thickness in actual production based on application. Moreover, if they know the application is not critical, then they lower the thickness and supply lined pipes and fittings at a lower cost.
In such a case, the corporate buyer may feel a sense of satisfaction in procuring apparently high-quality products at exceptionally discounted rates. However, the buyer likely lacks awareness about the actual lower-grade materials being supplied due to cost-cutting shortcuts taken by the supplier. Additionally, conflicts of interest arise when long-standing relationships between plant maintenance teams and suppliers result in the acceptance of inferior materials that should have been rejected for non-compliance.
In PTFE / PFA / FEP / PVDF lined Pipes and fittings and valves, around 70-80 % cost is fluoropolymer material. Now, for example, in the case of 4 mm thickness, if any manufacturer offers a lined product with 3 mm thickness, then they will save almost 25 % cost of fluoropolymers. As a result, there could be a chance for big savings, but at the same time, the possibility of product failure and shorter life will be much more than someone’s imagination.
Buyers may feel satisfied getting a discounted price when placing the order. Still, they likely do not realise that the shorter lifespan of such discounted products means they will need to replace them twice as often compared to quality products that come at a slightly higher upfront cost.
In big chemical projects and pharma plants, most of the consultants and engineers specifically demand PFA in lined fittings and valves because of its high-temperature applications and the long life of lined equipment.
Some manufacturers/processors use 40-50 % less cost of FEP than PFA for their gain. Now, in order to save 40-50% on material cost, they use FEP instead of PFA in the product where 70-80% cost in finished products is actually the cost of fluoropolymer.
These manufacturers take advantage of knowing how the product will be used by the customer. For example, if they know the fittings and valves are going into a pharmaceutical plant that runs at about 100°C, they will use the cheaper material FEP instead of the specified PFA. They assume FEP will not fail often at that temperature. If some FEP parts do end up failing, the manufacturers expect to keep the customers happy by giving them free replacement parts. This avoids fixing the problem of using the wrong material in the first place.
During price negotiations, purchasers may feel satisfied getting exceptionally discounted pricing by believing they will receive PFA-lined products meeting the technical specifications. However, they receive FEP-lined products instead of the specified PFA-lined products - exploiting the difficulty for purchasers to catch this material substitution.
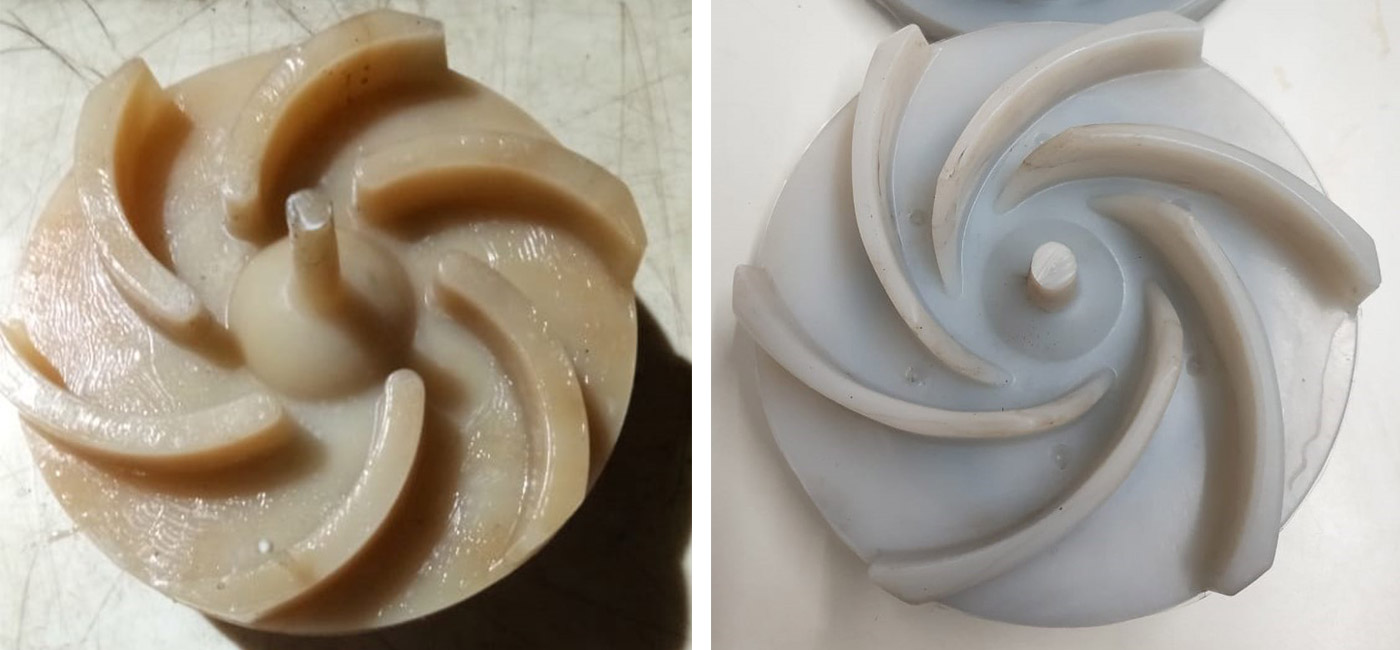
During production, parts sometimes fail during quality checks, leading to wasted fluoropolymer material. Similarly, excess material is often trimmed away after the lining process. Some manufacturers save these leftovers and repurpose them into smaller components, such as balls in ball valves, plugs in plug valves, or elements-inline strainers. Therefore, the quality and performance of the final product depend on the condition of these low quality materials.
RAM-extruded PTFE liners cost less than paste-extruded PTFE liners. Therefore, some manufacturers use the cheaper RAM-extruded liners in small-diameter pipes to save money. They assume customers will not notice the substitution.
But internationally, paste-extruded PTFE is recommended for pipelining. This is because paste-extruded PTFE resists chemicals passing through better than RAM-extruded over time. This property, called permeability, is very important.
Over time, chemicals permeating through PTFE liner and reaching metal surfaces underneath cause corrosion and contamination. This leads to issues of leakage, unexpected maintenance, poorer processed quality, and even fire or spills.
For PTFE-lined pipes, liner lifetime depends on both mechanical strength and how well it blocks chemicals. Though RAM-extruded is cheaper, paste-extruded PTFE blocks chemicals better. Cutting corners to just save money without understanding application needs is risky.
In essence, RAM extrusion cuts costs, but paste-extruded PTFE is a global best practice for chemical resistance and blocking leaks. We advise against trading off permeability for invisible savings when equipment and plant safety are at stake.
Recommendations for Buyers
While this article highlights practices employed by some companies, our intention is not to accuse or single out any specific manufacturer. We understand that companies aim to balance quality with cost-effectiveness in order to stay competitive. However, transparency and open communication with customers is key.
Even if buyers do not request intricate production details, suppliers should take it upon themselves to guarantee that their products meet all specifications. This not only builds trust but also helps ensure safe and long-lasting equipment performance. Ultimately, every manufacturer's commitment should be to supply products designed and built to deliver maximum safety for the intended operating life.
Unfortunately, we have witnessed accidents at chemical and pharmaceutical plants where substandard lined equipment contributed to fires, leaks or explosions. While the true cause may be hidden, poor-quality linings likely played a role. We hope that increased awareness and dialogue within the industry can help avoid such incidents moving forward.
Explore Our Industrial Fluoropolymer Applications
- PTFE Lined Products
- PTFE Lined Dip Pipes
- PFA Lined Valves
- PTFE Products
- PTFE Lined Pipe
- PTFE Lined Bend
- PTFE Lined Reducer & Reducing Flange
- PTFE Lined Tee/Cross
- PFA lined Instrument Tee
- PTFE Lined Sight Glass
- PTFE Lined Dip Pipes
- PFA Lined Ball Valve
- PFA Lined Plug Valve
- PFA Lined Diaphragm Valve
- PFA Lined Butterfly Valve
- PFA Lined Flush Bottom Valve
- PTFE Expansion Joints / PTFE Bellows
- PTFE Liner / PTFE Tubes
- PTFE Sheet